硫化机合模速度慢,硫化机合模力
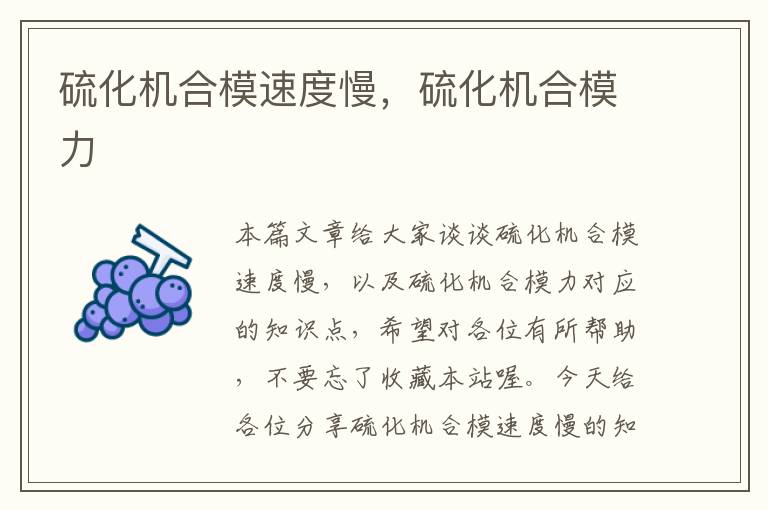
本篇文章给大家谈谈硫化机合模速度慢,以及硫化机合模力对应的知识点,希望对各位有所帮助,不要忘了收藏本站喔。 今天给各位分享硫化机合模速度慢的知识,其中也会对硫化机合模力进行解释,如果能碰巧解决你现在面临的问题,别忘了关注本站,现在开始吧!
1、橡胶练橡硫变慢是什么原因?
变形:原因可能是制品冷却不充分,硫化速度过慢,以及制品脱模后处理不当等。解决办法包括改进冷却方法,降低硫化速度,改善制品脱模后的处理方法等。欠硫:原因可能是硫化时间不够,硫化温度偏低,以及胶料配方不合适等。
有几种可能,一是欠硫,二是有杂质,三是胶料配方问题。
原因: 硫化不足。 压力不足。 模内或胶料中有杂质或油污。 硫化模温过高。 硫化剂加少了,硫化速度太慢。解决方法: 加压 加长硫时 调整配方,加快硫化速度。 多排气。
橡胶硫化排气问题 在橡胶制品的硫化过程中,橡胶内部的气体会被加热膨胀,形成微小的气泡。这些气泡如果不能及时排出,会导致橡胶制品的质量下降,比如出现麻点或气泡。因此,排气是橡胶硫化过程中非常重要的一环。
影响胶料硫化质量的主要因素主要有两方面:1)硫磺用量。硫磺用量少,硫化形成的多硫键少,弹性差,耐撕裂性能差,但硫化胶不容易返原,耐候性好。硫磺用量多,弹性好,但胶料容易返原,耐候性也变差。2)促进剂。
2、63.5寸硫化机合模力拉不起来电机电流过大怎么处理
对于小型电动机,空载电流只要不坡过额定电流的 50% 就可以继续使用。问题三:异步电机空载电流大是什么原因 异步电机空载电流大:.轴承损坏、缺油. 气隙过大或不均匀;更换新转子或调整气隙 转子与定子摩擦轴承过紧。
一,减小负荷,不要小马拉大车;二,还可以试验着适当减小启动电容;三,电机有问题,换新。
电源电压过低 电源电压过低时,若电动机的电磁转矩保持不变,磁通将降低,转子电流相应增大,定子电流中负载电源分量随之增加。
你好: ——★电动机维修、拆除绕组时,需要加热旧线圈。大型正规企业采用线圈通电加热的方法,线圈软化后、拉出(铁心不会过热);而普通小型企业,多采用火烧的方法,以节约费用(省电)。
3、硫化机手动不行自动可以
及时维修。橡胶硫化机,适用于压制各种成型产品由PLC控制,计算机自动检测系统,人性化的程序设计,可自动完成合模,强制开模,移模,硫化定时。
胶板在硫化过程中,需要对胶板施以一定的外力,这个外力是根据工况不同改变的,但这个最大值是硫化机的一个重要参数。一般是以KN或Kg表示。
压力不足、密封件失效。压力不足:液压系统中油路堵塞或压力不足。密封件失效:辅缸密封件磨损或老化,导致密封不良。
就算是自动的,仍然需要手工放料和手工取产品。现有的模具可能还不配套。
高压泵部分磨损 2,高压溢流阀损坏 3,换向阀泄漏 4,液压缸串缸 5,管接头泄漏 高压时流量小,引起的原因多的。
4、橡胶硫化出现变焦,有小孔,裂痕是什么原因
缺胶憋气造成的,看填料方式,尽量不要有表面缺胶。硫化是多排几次气体或抽真空。再不行就降低温度延长硫化时间试试。
硫化橡胶产品时有裂痕是说明硫化温度高,料流动性不好,焦烧时间太短,胶料部分焦烧致使出现裂痕。硫化橡胶指硫化过的橡胶,具有不变黏,不易折断等特质,橡胶制品大都用这种橡胶制成。也叫熟橡胶,通称橡皮或胶皮。
开裂的原因大概以下几种: 硫化速度太快,胶流动不充分。 模具脏或胶料粘污迹。 隔离剂或脱模剂太多。 胶料厚度不够.橡胶接头早制造过程中采取的措施一般如下:降低模温,减慢硫化速度。保持胶料.模具清洁。
橡胶产品引起裂纹的原因是未改进胶料配方和改进硫化工艺条件。
5、轮胎硫化机造成不合模几种常见原因
可能的原因有多种,你可以挨个排除下:平板硫化机故障。脱模剂未加或者硫化温度过高(脱模剂分解)。模具不合理,没有溢料槽,和溢气槽,压完后产品吸在模具上了。
A、处置环节 即整套硫化机存在设计缺陷或是局部环节处理不力。B、水份 硫化当中不可避免因蒸汽冷却或降温时有一定的水分,导致轮胎硫化机上下模具的蒸汽含水量不尽相同,直接导致上下模具的温差。
⑵相应部位的胶料由于某种原因造成加工温度过高,该部位胶料焦烧时间短。⑶部位过渡设计不合理,或被过度拉伸变形,影响排气。⑷硫化模具不洁净或排气孔堵塞。⑸硫化模具排气孔位置不合理或数量不够。
由于硫化机为金属材质,硬度较高,在生产运行过程中受到振动冲击和其他复合作用力,导致部件形成间隙,造成磨损。
另外,给以足够的压力防止模具离缝面出现溢边、花纹缺胶、气孔海绵等现象。连杆、曲柄齿轮等主要受力件上的运动副,是由铜套组成的滑动轴承,易磨损,对精度影响较大。
关于硫化机合模速度慢和硫化机合模力的介绍到此就结束了,不知道你从中找到你需要的信息了吗 ?如果你还想了解更多这方面的信息,记得收藏关注本站。 硫化机合模速度慢的介绍就聊到这里吧,感谢你花时间阅读本站内容,更多关于硫化机合模力、硫化机合模速度慢的信息别忘了在本站进行查找喔。
[免责声明]本文来源于网络,不代表本站立场,如转载内容涉及版权等问题,请联系邮箱:3801085100#qq.com,#换成@即可,我们会予以删除相关文章,保证您的权利。 转载请注明出处:http://www.wsfkq.cn/pqzz/15747.html