硫化机合模缓慢-硫化机不合模有哪些原因
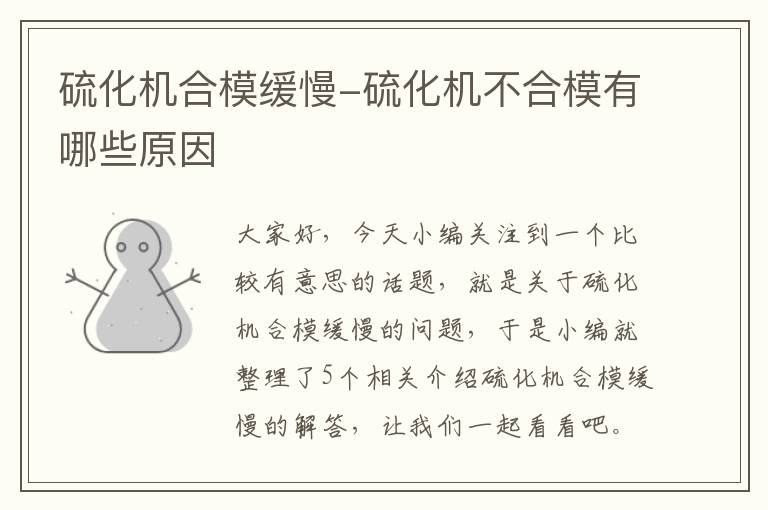
大家好,今天小编关注到一个比较有意思的话题,就是关于硫化机合模缓慢的问题,于是小编就整理了5个相关介绍硫化机合模缓慢的解答,让我们一起看看吧。
- 硫化机锁模太慢是什么原因造成的?
- 轮胎硫化机造成不合模几种常见原因
- 硫化机合模,压力上去,不硫化,是什么原因?
- 63.5寸硫化机合模力拉不起来电机电流过大怎么处理
- 平板硫化机动作缓慢,压力表没压力是怎么回事?
1、硫化机锁模太慢是什么原因造成的?
密封圈损坏。解决方法:检查具体是哪个密封圈损坏,进行更换即可。硫化机一种对各种橡塑制进行硫化的机器,具有定时锁模、自动补压、自动控温、自动计时、到时报警等功能。
电压不足,或是机器老化了。硫化机是一种对各种橡塑制品进行硫化的机器,具有定时锁模、自动补压、自动控温、自动计时、到时报警等功能。硫化机分电加热、蒸汽加热和导热油加热三种形式。
二板导轨及哥林柱磨损大,检查二板导轨及哥林柱,更换二板铜套,哥林柱,加注润滑油。2):开锁模速度压力调整不当,设定流量20,压力99时锁模二板不应爬行,调节流量比例阀孔,或先导阀孔,调整比例阀线性电流值。
硫化机同其他工具一样,在使用过程中会出现一些小的问题,这些问题有的是由于使用不当,有的是因为保管过程不当导致,这些小的问题,都可以即时解决,不影响机器的正常使用。
2、轮胎硫化机造成不合模几种常见原因
可能的原因有多种,你可以挨个排除下:平板硫化机故障。脱模剂未加或者硫化温度过高(脱模剂分解)。模具不合理,没有溢料槽,和溢气槽,压完后产品吸在模具上了。
A、处置环节 即整套硫化机存在设计缺陷或是局部环节处理不力。B、水份 硫化当中不可避免因蒸汽冷却或降温时有一定的水分,导致轮胎硫化机上下模具的蒸汽含水量不尽相同,直接导致上下模具的温差。
⑵相应部位的胶料由于某种原因造成加工温度过高,该部位胶料焦烧时间短。⑶部位过渡设计不合理,或被过度拉伸变形,影响排气。⑷硫化模具不洁净或排气孔堵塞。⑸硫化模具排气孔位置不合理或数量不够。
由于硫化机为金属材质,硬度较高,在生产运行过程中受到振动冲击和其他复合作用力,导致部件形成间隙,造成磨损。
另外,给以足够的压力防止模具离缝面出现溢边、花纹缺胶、气孔海绵等现象。连杆、曲柄齿轮等主要受力件上的运动副,是由铜套组成的滑动轴承,易磨损,对精度影响较大。
3、硫化机合模,压力上去,不硫化,是什么原因?
它上下两面有加热板,温控电加热,大约140度,硫化40分钟。
可能的原因有多种,你可以挨个排除下:平板硫化机故障。脱模剂未加或者硫化温度过高(脱模剂分解)。模具不合理,没有溢料槽,和溢气槽,压完后产品吸在模具上了。
加温不显示 ① 可能原因是电流表坏了 ② 可能是加热管有损坏 观察控温仪指针情况,如指针顺时针转到底,说明热电阻接线断路或热电阻烧断。
合模不到位。合模不到位、限位开关没合或失灵、汽室密封圈老化损坏或错位,均能造成外压蒸汽密封圈处泄漏,都会造成无信号的。
4、63.5寸硫化机合模力拉不起来电机电流过大怎么处理
对于小型电动机,空载电流只要不坡过额定电流的 50% 就可以继续使用。问题三:异步电机空载电流大是什么原因 异步电机空载电流大:.轴承损坏、缺油. 气隙过大或不均匀;更换新转子或调整气隙 转子与定子摩擦轴承过紧。
一,减小负荷,不要小马拉大车;二,还可以试验着适当减小启动电容;三,电机有问题,换新。
电源电压过低 电源电压过低时,若电动机的电磁转矩保持不变,磁通将降低,转子电流相应增大,定子电流中负载电源分量随之增加。
你好: ——★电动机维修、拆除绕组时,需要加热旧线圈。大型正规企业采用线圈通电加热的方法,线圈软化后、拉出(铁心不会过热);而普通小型企业,多采用火烧的方法,以节约费用(省电)。
5、平板硫化机动作缓慢,压力表没压力是怎么回事?
从油泵往后的一些油路元件有没有漏压的,比如溢流阀、调压阀、角阀、顺序阀之类的;因为油路上的阀,安装时都有密封圈,如果密封圈损坏,肯定打不上去,即使上去了,一会就下来了。
确定高压阀有没开启。如果有开就在看溢流阀。2。确定溢流阀是不是有问题,用潜换法就可以很快就确定了。3。
① 可能原因是电流表坏了 ② 可能是加热管有损坏 观察控温仪指针情况,如指针顺时针转到底,说明热电阻接线断路或热电阻烧断。
原因电镀耐酸碱过滤机的排气阀有块状异物导致排气阀闭塞,没有压力显示。办法:用方便的工具,如开水,螺丝刀,电钻等方法,将排气阀打通,使过滤机的压力表显示正常。
到此,以上就是小编对于硫化机合模缓慢的问题就介绍到这了,希望介绍关于硫化机合模缓慢的5点解答对大家有用。
[免责声明]本文来源于网络,不代表本站立场,如转载内容涉及版权等问题,请联系邮箱:3801085100#qq.com,#换成@即可,我们会予以删除相关文章,保证您的权利。 转载请注明出处:http://www.wsfkq.cn/pqzz/14472.html